Refined Sheet Metal Fabrication for 3D Printing in the Aerospace and Medical Sectors
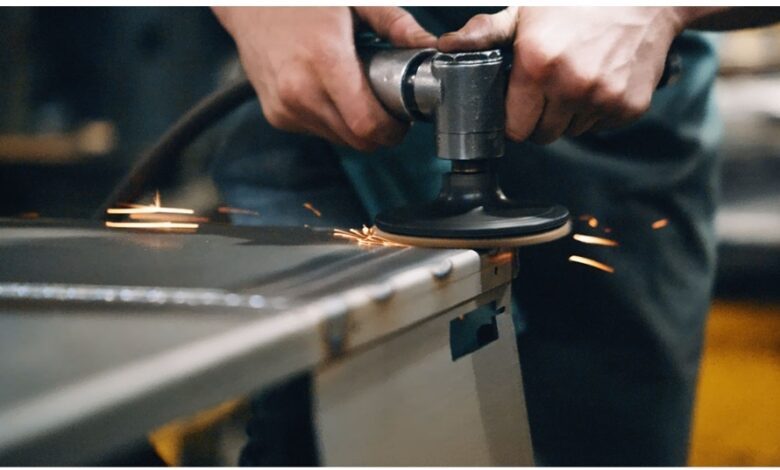
Modern printing technology that has found its way into the aircraft manufacturing industries and the medical world is 3D printing which offers a streamlined way of developing perfect parts with intricate features. An important element in this process to point out is the incorporation of improved sheet metal fabrication that forms a structural framework and functional durability needed in these aggressive industries. To the companies in these sectors, therefore, identifying the most qualified sheet metal manufacturing companies, and custom sheet metal fabricators to work with to meet these industry needs and produce creative designs is crucial.
Importance of Precision in Sheet Metal Fabrication
Accuracy is the fundamental component of high-quality sheet metal working, especially within high-stake markets such as aviation and medical sectors. Currently, sheet metal acts as the base form for many components printed through 3D technology, with applications in airplane components, manufacturing equipment, and even surgical tools.
Key aspects of precision fabrication include:
– Tight Tolerances: Aerospace and medical fields require very close tolerances to guarantee any component will work correctly under high risk conditions.
– Advanced Materials: Industrial applications include Aluminum Titanium, Stainless steel, and others popular for their strength, corrosion resistance, and biocompatibility.
– Customization Options: Due to its applicability depending on the needs of a particular design and the type of application, sheet metal fabrication is among the most suitable to be used together with 3D printing.
For businesses, hiring a custom sheet metal fabricator guarantees an opportunity to access the correct skills and high technologies to develop parts that conform to a business’s specifications.
Advantages for the Aerospace Sector
In the aerospace industry where the components must be strong enough to withstand different types of pressure both pressure and shear, Sheet metal fabrication forms the backbone in the third dimension printing. Combining additive manufacturing with fabricated metal parts enhances both structural integrity and functionality, offering several advantages:
– Lightweight Design: Inefficient designs of fabricated sheet metal components can be further refined to lightweight without compromising on durability, thereby leading to fuel conservation and enhanced performance of the aircraft.
– Thermal Resistance: There are several industries where the material used has to endure high temperatures: Aerospace. Titanium or stainless steel materials are used for the resistance to rough use since some of the products may need to be durable.
– Streamlined Production: Combining sheet metal fabrication with 3D printing leads to time and cost savings resulting in quick delivery of quality parts.
Therefore by working with seasoned sheet metal manufacturing companies, various aerospace businesses can harness these benefits in containing probable dangers, within a dynamic industry.
Benefits for the Medical Sector
The life of the medical industry depends on the accuracy and dependability of tools, devices, and implants making sheet metal fabrication an essential part of printers. Advanced production processes guarantee that medical components possess acceptable levels of cleanliness, bio-compatibility and operational performance necessary for the medical sector.
Key benefits for medical applications include:
– Biocompatibility: Among the metallic materials, steel and titanium are favourable for most medical applications because they do not react with body fluids and are resistant to corrosion.
– Hygienic Design: Fabrication processes enable the creation of substrate surfaces with in-dimensions smooth and free from contaminating particles which can easily be sterilized to minimize instances of infection.
– Customization for Patient-Specific Needs: When 3D printed with sheet metal forming, implants, prosthesis, and even surgical instrumentation can be made to fit anyone, anywhere.
This is why medical businesses should work with quality sheet metal fabricators to get high tolerance and medical quality parts.
Advanced Fabrication Techniques
The past decade’s advancements in sheet metal fabrication assist the equipment to continually handle the new challenges of 3D printing in aerospace and medical industries. These complex procedures refine the quality, rate, and accuracy of the formed parts which are suitable for incorporating into additive manufacturing systems.
Common techniques include:
– Laser Cutting: Allows the conformal fabrication of the part under consideration to the shape of complicated three-dimensional printed molds.
– CNC Machining: Manufactures parts with thin walls hence creating minimal gaps in the joining faces of other parts.
– Forming and Bending: It also cuts out metal shapes for its clients according to the specifications of application in aerospace industries and medicine.
– Surface Finishing: Fine working and buffing help achieve flat surfaces ideal for medical equipment cleanliness plus control of surface ripple on aerospace items.
Through the employment of these sophisticated fabrication techniques, the sheet metal manufacturing companies are in a position to deliver the quality parts that are the foundation to the new age 3D printing projects.
Choosing the Right Fabrication Partner
Choosing the right sheet metal manufacturing companies and the right custom sheet metal fabricators part is essential for the aerospace and medical businesses that want to improve their 3d printing processes. Skill in the creation of specific parts of lamps should be checked periodically to be sure that the quality and specialization of the lamps are met consistently; having a competent partner can ensure the consistent quality of work, adherence to industry standards and design requirements.
When evaluating potential partners, consider the following factors:
– Industry Experience: Search for fabricators with prior experience in aerospace and medical industries since they are sensitive industries to work with.
– Certifications: Make sure that your company has necessary approvals; for instance, it is approved to produce and sell medical devices, it has ISO 13485 certification or it deals with aerospace products, thus it is approved AS9100.
– Customization Capabilities: Select a material maker affiliated to your requirements and operations of a given business as well as the detailed demands of several application forms.
– Technology and Equipment: Check that the company has the ability to utilize advanced technologies like laser cutting and computer numerically controlled cutting machines in order to produce high end work.
– Commitment to Quality:Thus, high–reliability is a critical quality assurance necessity that can meet the demands of aerospace and medical industries.
It means that when connecting with the proper specialists, it is possible to increase numerous business aspects associated with stages of production, minimization of expenses, and optimization of the relevant 3D-printed parts.
High quality sheet metal works are a key driver in the success of 3D printing for aerospace and medical industries. With the application of both fabricated metal, concerning the strength and stability, and the additive manufacturing concerning accuracy and versatility, business can design new parts that will fully satisfy the requirements of these industries.
Manufacturing of light aircraft parts or even personalised medical devices requires the knowledge of sheet metal manufacturing companies and custom sheet metal fabrication companies. Using today’s technology and materials can enhance fabrication abilities to deliver precision, durability and specific requirements that are necessary to gain a competitive edge in these specialized industries. The future is bright as long as organisations embrace the right technologies and the right partners that will complement their strategies in business.