Precision CNC Machining in Medical Device Manufacturing: What You Need to Know
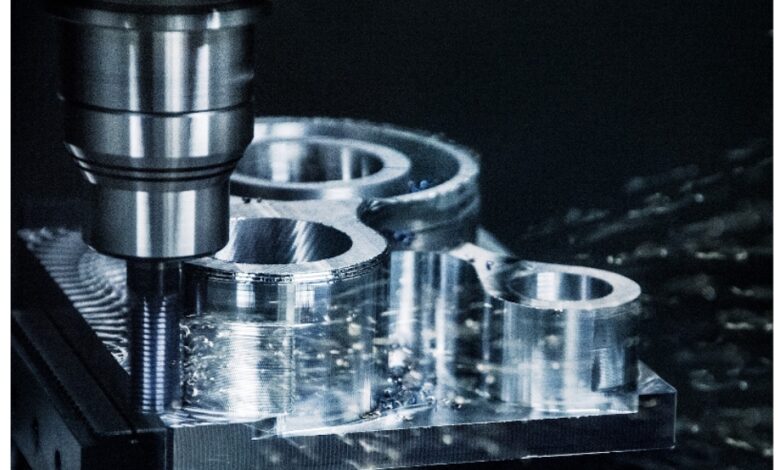
Companies operating in the medical device manufacturing industry must adhere strictly to precision and reliability. CNC machining is a central thread when it comes to the production of medical components in view of the strict standards required in the manufacturing process. Many of the applications involving the manufacturing of both surgical instruments and implantable devices require the use of precision cnc machining in an effort to produce accurate, reliable, and safe parts of devices. The CNC machining process will form the core discussion of this article in relation to medical device manufacturing and why B2B organizations cannot afford to ignore it.
The Role of CNC Machining
Computer Numerical Control or CNC machining remains the most popular technology for developing medical devices because it can generate very fine and complex parts and features. It includes the use of computer-interfaced tools to shape articles out of a solid mass to produce the desired part.
Why CNC Machining is Vital in Medical Device Manufacturing:
– Precision: Using CNC machines, tolerances can be increased to as little as the microns which makes every component fit and to meet its expected function.
– Versatility: With an ability to handle an extensive range of materials, including stainless steel, titanium as well as advanced polymer, CNC machines satisfy the medical industry’s variety needs.
– Reproducibility: EFFECT : It is also important for the mass production of the medical components because CNC machining maintains the quality during the production runs.
To manufacturers that are engaged in sourcing of medical elements from such areas as China machining suppliers, CNC machining offers the necessary stability and growth that is expected in production processes so that the quality of the parts produced is not compromised.
Uses in Medical Equipment
High accuracy cutting is applied to produce numerous kinds of medical products and equipment. Need for these devices has therefore grown greatly due to improvement in the healthcare sector and the addition of minimally invasive surgical instruments and equipment.
Key Applications Include:
– Surgical instruments: Knives, tweezers and other related instruments need to have a fine edge to enable it to accomplish functions properly in surgeries.
– Orthopedic implants: Bone screws, plates and joint replacement prostheses with complex geometries can be fabricated employing the CNC machining.
– Dental implants: Titan implants can only be categorized as very delicate in that they demand very close fitting within the patient’s mouth.
– Diagnostic devices: Subsystems and assemblies of imagers and diagnostic equipment are frequently made from small intricate subsystems.
– Prosthetics: Prosthetic limb that is fit made from lightweight durable materials through computer numerical control machining technology.
These applications illustrate that CNC machining is crucial for creating parts that go beyond the requirements needed to serve the medical field.
Benefits on Medical Manufacturing
There are quite a number of benefits, which can be attributed to cnc machining making it suitable for use in the production of medical devices. Due to the capability to create various geometries in products, in addition to the level of precision, the technology can suit the medical industry’s requirements.
Key Advantages Include:
– High precision and accuracy: Due to its versatility the teeth profiles of most medical devices can be very complex and have strict tolerance requirements that are a cinch to meet with use of CNS machining.
– Material flexibility: CNC machines can use bio compatible materials like titanium, stainless steel and PEEK which are suitable for implantable products.
– Scalability: CNC Machining is not limited to production type as the process can easily be used for prototype production or large scale production.
– Quick turnaround times: CNC reduces overall production lead times and the devices are brought to market as soon as possible.
– Regulatory compliance: Due to the precision of the CNC machining, some manufacturers can adhere to regulatory specifications that are mandatory in the medical field.
These are some of the benefits that one will get with the CNC milling companies who deal with the medical device industry solutions providers.
Choosing the Right CNC Partner
Indeed it can be said that for B2B organizations in the medical device industry, choice of CNC machining partner is crucial. The expert skills and knowledge, and a general awareness of regulations of the partner can greatly affect the quality and efficiency of the deliverable devices.
What to Look for in a CNC Machining Partner:
- Experience in medical manufacturing: The machining partner needs to possess good experience in manufacturing medical parts and they must meet relevant standards of the industry.
- Advanced equipment: Today’s modern CNC machines capable of performing multiple axes are critical in manufacturing the intricate medical parts.
- Material expertise: The partner should have prior experience using materials that are biocompatible which are prevalently used in production of medical devices.
- Regulatory knowledge: FDA, ISO 13485, and other medical device requirements are met during production due to understanding of them.
- Global sourcing capabilities: Many firms seeking for either higher quality or cheaper offer seek CNC suppliers in places such as China machining centers.
In choosing a reliable CNC partner, B2B clients do not only expect their suppliers to produce high quality components but also to offer design and inexpensive manufacturing services.
Future Trends in CNC Machining
This paper identifies the current opportunities and threats that define the emergence of future transformations of conventional and computer numerical control machining in the medical device manufacturing industry. Keeping tabs on these trends will be important to B2B companies that are aspiring to thrive among an increasing number of competitors in the global market.
Emerging Trends Include:
– Automation and robotics: The coupling of robotics with cnc machines has enhanced production efficiency thus lowering the cost of labour.
– Additive and subtractive hybrid manufacturing: CNC machining when integrated with 3D printing offers the best solution due to its advantages in complex geometries and minimum waste.
– Micromachining: Another consequence of current trends in miniaturizing medical devices and making them more complex is the growing use of CNC micromachining technologies for fabrication of miniscule but accurate components.
– Sustainability initiatives: today’s CNC milling companies are taking environment conscious measures namely on the recycling of metallic materials and on energy conservation on the production machines.
– Smart manufacturing:Networking of CNC machines makes analysis of real time data for predicting failures, control over the quality of product and, even over product quality of products possible.
Such improvements will only advance the capabilities to offer innovative and highly efficient manufacturing service for the B2B sector products such as medical devices.
CNC precise machining has revolutionized medical device manufacturing technology, where it is now possible to produce medical components and devices with high accuracy and solidity. Whether machining components used in surgery or inserting elements into the body, the intricacy of the medical industry requires parts that are manufactured to perfection by CNC machining.
To B2B companies, collaborating with those skilled CNC milling firms or incorporating the know-how of preferred supplying nations like China machining centers may be a beneficial solution to this problem. With time the applicability of the CNC machining in the medical manufacturing will expand beyond what is seen; thus, it is poised to deliver more in terms of innovation in meeting patients needs.