How to Choose the Right Pneumatic Ball Valve for Your Project
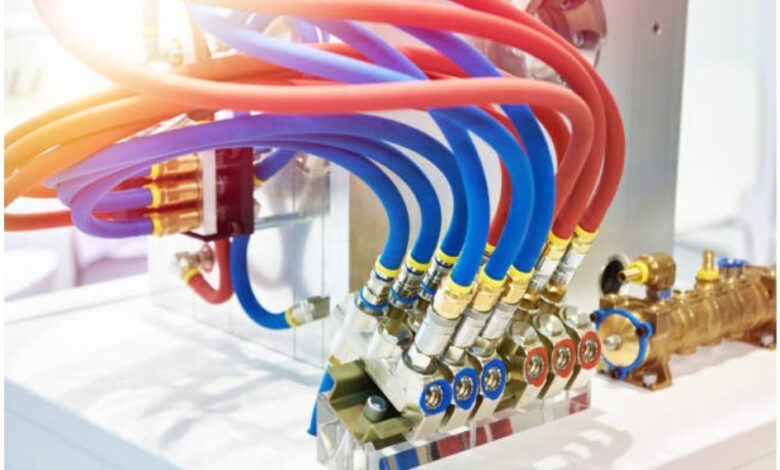
When choosing the correct pneumatic ball valve for your project there are several factors that must be taken into consideration in order to achieve the correct efficiency and durability level. In the oil and gas production industry, chemical processing, food and beverage and water treatment pneumatic ball valves offer a convenient flow control method. Yet, a wrong selection of a control valve results in poor performance, frequent maintenance expenses, and subsystem failure. Having a close relationship with an electrical valve manufacturer or a pneumatic ball valve company can guide you through the required steps and offer the best fitting valve for your needs.
Know More about the Particulars of You Project
The first thing to look at before deciding to purchase the pneumatic ball valve is to understand what your project demands. Some considerations are the type of media within which the valve will operate, this includes the types like liquid, gas or even corrosive media. For example if the media is abrasive or corrosive it will be necessary to use a valve having body and trim members fabricated of stainless steel or other materials incorporating PTFE lined parts.
Further, remember the working conditions, often pressurized, the temperature, pressure, and the flow characteristics. Compressors will come under high pressure; thus, valves must be of a kind that can work under high pressure without leakage or failure. Likewise, there may be conditions of temperature variations that would require the putting of materials and seals to thermal cycling. It is recommended to seek help from an electric valve manufacturer with rich experience or a pneumatic ball valve supplier to choose this kind of valve that meets the above critical characteristics and will not affect its performance in the long run.
Assess Construction of Material and Stability
It is therefore important to look at aspects such as the material construction of a pneumatic ball valve. The material should be able to seamlessly interact with the media it will regulate because its formation could be through corrosion or degradation with time. The materials that can be used for manufacturing of pneumatic ball valves are stainless steel, brass, PVC, and carbon steel, but they are not identical in some way as they have their special features for a certain type of work.
For instance, the stainless steel valves have very less rate of corrosion; hence they are most suitable for chemical manufacturing companies or food and beverages manufacturing companies. PVC valves are comparatively light weight and also cheaper and less resistant, so they are best for low pressures. When purchasing Pneumatic Ball Valve from the factory, its Material Quality requirements, and quality Check Points should adhere to its durability under the service condition of the project.
Choose the Right Actuation Mechanism
Pneumatic ball valves work based on compressed air hence making actuators to operate at high speed. Nonetheless, according to the applications you have for your particular project, you should consider the kind of actuator mechanism to use; whether it is the spring-return or the double-acting one.
Spring-return actuators provide the designated valve with additional safety since it repositions itself to the default state when air pressure is released. Double acting actuators however, need compressed air to function opening and closing the valve and are used with more elaborate systems.
Always seek advice from an electric valve manufacturer in case of valve selection because he or she will recommend the most appropriate actuator for the system from among pneumatic ball valve actuators or others. Also, ensure whether the operation of the valve needs the extra functionality like manual override, limit switch or positioner for better operation and control of the whole system .
Assess the Valve’s Size and Flow Requirements
One should also consider the size of the valve and its flow rate ability added to that consideration. The size and Cv of the valve define the efficiency of the control of the flow rate of the media through the system. Small valves could hinder flow while large valves are costly in terms of both control variations and unnecessary flow.
To choose the correct size used for the selection of the valve, determine the flow rate needed for your system and compare the two against the valve’s Cv number. This issue should be also taken into account when deciding the pipe size, speaking about pressure drops and line velocities. When you buy a valve from a pneumatic ball valve factory, you know you will always have many options in terms of size and type of the valve you require for your project.
Select a Reliable Manufacturer Or Supplier
However, one of the best strategies to consider when selecting on the right pneumatic ball valve is selecting the right manufacturer/supplier. When approaching an electric valve manufacturer or pneumatic ball valve supplier, customers can expect to receive only high quality products and adequate technical support on this process.
Ensure to make sure that the manufacturer you select has the right experience and offers dependable and sturdier valves for your market. They ought to also offer detailed literature features concerning the product such as the detailed features of the product, installation procedures as well as they should provide me with maintenance manuals in order to help me get the best out of the product. Furthermore, a supplier who can provide customization services makes certain that the valve meets the innovation of the project .
By working with a reliable pneumatic ball valve factory, not only do you get excellent quality valves, but you get long-term support for your system, thus making your project more effective and economic.
Accordingly, the need to choose a right pneumatic ball valve entails understanding; the project requirement, materials and durability, actuation mechanism, and the manufacturer/supplier. When it comes to electric valves or pneumatic ball valves, you really need to work with a supplier or manufacturer to make sure your valve fits the need and requirement, increase efficiency, and durability. Consulting with professionals delivers the best results that you can be sure will meet your project needs appropriately.