The Role of GMP-Compliant Blending Facilities in Ensuring Product Safety
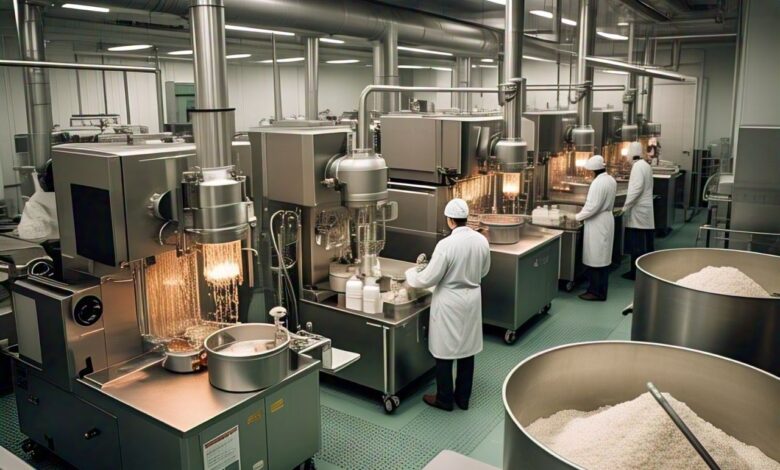
In the pharmaceutical, food, and supplement industries, ensuring product safety and quality is paramount. Any deviation in formulation, contamination, or inconsistency can lead to adverse health effects or regulatory non-compliance. One of the most crucial steps in the manufacturing process is blending, where different ingredients are mixed to create a uniform and effective final product. To maintain the highest quality standards, GMP-compliant blending facilities play a key role in ensuring that all manufacturing processes adhere to Good Manufacturing Practices (GMP).
What Are GMP-Compliant Blending Facilities?
GMP (Good Manufacturing Practice) regulations are a set of guidelines designed to ensure products are consistently produced and controlled according to established quality standards. These guidelines, enforced by regulatory agencies such as the FDA (Food and Drug Administration) in the U.S. and EMA (European Medicines Agency) in Europe, are essential in preventing errors, contamination, and deviations in the manufacturing process.
GMP-compliant blending facilities refer to manufacturing plants that adhere to these rigorous standards while mixing raw materials into a homogenous product. These facilities implement stringent protocols for equipment cleanliness, material handling, documentation, and personnel training to maintain safety and quality control throughout the blending process.
The Importance of GMP Compliance in Blending
Blending is a crucial process in the production of pharmaceuticals, food products, and dietary supplements. The accuracy of ingredient proportions, uniformity of the blend, and prevention of cross-contamination directly impact the final product’s safety and efficacy. GMP compliance ensures that each batch of blended material meets regulatory standards and consumer safety expectations.
1. Consistency and Uniformity
A key objective of blending is to ensure the uniform distribution of active ingredients and excipients (inactive substances) within a mixture. GMP guidelines mandate precise measurements, validated mixing techniques, and batch testing to ensure product consistency. Without GMP compliance, inconsistencies in the blend could lead to variable potency, ineffective products, or harmful overdoses.
2. Preventing Cross-Contamination
Cross-contamination occurs when unintended materials or substances are introduced into a product. GMP-compliant blending facilities implement strict measures to prevent cross-contamination, such as:
- Dedicated equipment for different products to avoid residual contamination.
- Validated cleaning protocols to remove any remnants of previous batches.
- Airflow control systems to prevent airborne particles from contaminating different product lines.
- Physical barriers and zoning within the facility to separate different processing areas.
3. Quality Control and Testing
GMP regulations require continuous quality control (QC) measures throughout the blending process. This includes:
- Raw material testing before blending to confirm purity and compliance.
- In-process testing to monitor blend homogeneity and ingredient distribution.
- Finished product testing to ensure the final mixture meets all regulatory specifications.
By implementing rigorous quality control measures, GMP-compliant blending facilities identify and address any potential defects before the product reaches consumers.
Key Elements of a GMP-Compliant Blending Facility
For a facility to achieve GMP compliance, it must integrate several critical components into its operations.
1. Facility Design and Sanitation
GMP guidelines dictate that blending facilities must have a clean and well-maintained environment to ensure product safety. This includes:
- Smooth, non-porous surfaces to prevent microbial buildup.
- Temperature and humidity control to preserve ingredient stability.
- Designated zones for different production stages to prevent cross-contamination.
- Validated cleaning and sanitation procedures to eliminate residues.
2. Equipment Calibration and Maintenance
Blending equipment must be regularly calibrated and validated to ensure accurate mixing and uniformity. GMP facilities adhere to strict maintenance schedules and document all equipment performance checks to prevent unexpected malfunctions.
3. Personnel Training and Hygiene
Personnel working in GMP-compliant blending facilities undergo rigorous training in GMP protocols, including:
- Proper handling of raw materials and equipment.
- Adherence to hygiene standards, such as protective clothing and handwashing procedures.
- Understanding of Standard Operating Procedures (SOPs).
Trained personnel ensure compliance with quality and safety guidelines, minimizing human error in the blending process.
4. Comprehensive Documentation and Record Keeping
A fundamental aspect of GMP compliance is thorough documentation and record-keeping. GMP-compliant blending facilities maintain:
- Batch production records that track every stage of the blending process.
- Material traceability records that document raw material sources and lot numbers.
- Quality control logs that record testing results and corrective actions.
This level of documentation provides a clear audit trail, ensuring accountability and facilitating regulatory inspections.
Regulatory Compliance and GMP Certification
For a blending facility to be recognized as GMP-compliant, it must undergo regular inspections and audits by regulatory agencies. Certifications such as ISO 9001, cGMP (Current Good Manufacturing Practices), and NSF GMP Certification further validate a facility’s commitment to safety and quality.
Non-compliance with GMP regulations can lead to severe consequences, including:
- Product recalls due to contamination or quality failures.
- Regulatory fines and legal action.
- Damage to brand reputation and loss of consumer trust.
Thus, maintaining GMP compliance is not only a regulatory necessity but also a business imperative.
Conclusion
The role of GMP-compliant blending facilities in ensuring product safety cannot be overstated. By adhering to strict regulations, these facilities help maintain the integrity, quality, and efficacy of pharmaceutical, food, and supplement products. With comprehensive safety measures in place—ranging from facility design and equipment maintenance to personnel training and quality control—GMP compliance guarantees that consumers receive safe, reliable, and effective products.
For companies in highly regulated industries, partnering with a GMP-certified blending facility is essential to ensure compliance with industry standards and protect public health. Investing in GMP compliance is not just about meeting regulations; it’s about building trust, ensuring safety, and delivering excellence in every batch produced.