How Pneumatic Cylinders Enhance Industrial Automation
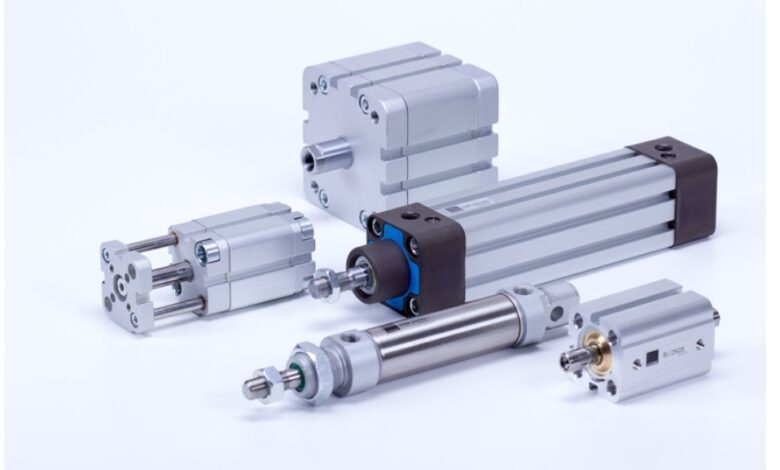
Pneumatic cylinders cannot be overlooked from the industrial automation systems as they are among the most significant pieces of automation equipment. Known also as air cylinders, these devices are crucial to convert compressed air into mechanical work and guarantee an optimal and accurate performance of most devices. This article discusses pneumatic cylinders and their contribution in industrial automation, the advantages accruing from their use, and why they constitute a key component of business systems.
What are Pneumatic Cylinders
Pneumatic cylinders are defined as mechanical actuators that develop force and motion through the use of compressed air in the form of a non-reciprocating air supply, and most commonly, linear-motion cylinders. They’re usually used in industrial automation processes or systems to push, pull, lift and hold components. Depending on the type of the pneumatic cylinders that are used, there are single acting, double acting, and the rodless type, and all these choices give business the solution they need.
Pneumatic cylinders can be integrated as a part of an industrial automation solution, to make processes more accurate and effective for businesses while consuming minimal energy. Despite the availability of sophisticated and expensive models, the uncomplicated nature of these bearings offers a strong reason for their popularity in many applications across different industries.
Accuracy and Speed in Movement Regulation
Perhaps, the most important strength of pneumatic cylinders used in industrial automation applications is their capacity for accurately controlling motion. Some types of automation systems imply the accurate positioning of the objects and constant working methods for manufacturing processes. Pneumatic cylinders bring this precision by giving the controllable force and speed needed in assembly line, packaging machinery, and material handling industries.
Cylinder’s types such as double-acting cylinders are common in industrial automation applications because of its requirement of both back and forth movements. These cylinders work under pressure on both bores of piston that give constant force to enhance its smooth working.
This precision not only adequately increases productivity but reduces errors making the pneumatic cylinders reliable in the automation industry for any organization with high standard quality output.
Portable from One Application to Another
The third advantage of using pneumatic cylinders is versatility of the cylinders. By having several types of designs as well as size and shape, they can be adjusted to fit various uses in industries. Here are some of the most common types of pneumatic cylinders and their uses:
– Single-acting cylinders: Suitable to use where force is typically required in one direction such as pressing or clamping jobs.
– Double-acting cylinders: Ideal for use where material has to reciprocate in both directions in an application such as in parcel handling or conveyors.
– Rodless cylinders: Ideal for any area in which it will be difficult to have enough room; for example, sliding doors or small machinery.
– Rotary cylinders: Used to support a shaft or axis that rotates, may be found in an indexing or turning application.
This versatility makes the pneumatic cylinder to be used in almost all the industrial automation solutions as industries can design their systems depending on the requirements of a task.
Energy Efficiency and Cost Saving
Originally, pneumatic cylinders were used as energy-saving mechanisms, and thus are cost-effective in organizations. Since these devices utilize compressed air as the major source of energy, the need for complicated electric circuitry is done away with, hence decreasing their energy demands and frequencies of breakdowns.
Furthermore, pneumatic cylinders make less contact with their environment since they are less complex in structure than hydraulic or electric actuators. As a result of its simplicity, operation cost reduces resulting in a better solution for automation systems since their maintenance is also relatively cheap.
For organisations who want to employ environmentally friendly solutions, pneumatic cylinders are also friendly in terms of energy consumption. The measure of energy cost of compressed air use decreases the generalistic energy impression of production procedures benefitting both environmental and financial conditions.
Durability in Hostile Climates
It is understood that working conditions in industrial areas are rather challenging, particularly tough working climate, dust, humidity, heat, and vibration. Pneumatic cylinders are created for such a type of environment which makes the product well suited for automation applications in hard environment zones.
For instance, stainless steel cylinders can perform well in an environment that causes high chances of moisture or chemical danger. Moreover, while using pneumatic cylinders there is not so much variation in performance as seen in hydraulic cylinders due to temperature effects.
This reliability helps the business to minimize the time they have to spend on routine maintenance and in the process, helps them maintain their operations on the right level, thereby recording high productivity.
Thus, as a timely shifting of the focus of industrial automation takes place, more and more companies embrace smart technologies. It also comes with improved monitoring methods that makes it easy to integrate with these advanced systems; Pneumatic cylinders.
For instance, today’s pneumatic cylinders are designed with some sensors that offer information on position, force, and the speed of the cylinder. These parameters can be input into a master control and used to anticipate problems and enhance the processes. Integration of pneumatic cylinders with IoT gadgets allows developing smart automation systems capable of enhancing the performance and providing information about the processes at enterprises.
This integration is a vital factor to industries if they are to cope with Industry 4.0 and remain relevant in the market. The appropriate industrial automation solution will help the business achieve the potential of pneumatic cylinders for improving its performance and efficiency.
Pneumatic cylinders are one of the most crucial parts of industrial automation processes since they provide numerous technical benefits for nearly all kinds of applications. Used on materials handling and assembly, small construction and equipment sizes, and in hostile environments, these devices deliver the force and motion control to accelerate production and reduce wastage.
Since there are numerous kinds of pneumatic cylinders, industries are able to design their applications according to their needs and at the same time take advantage of the advantages of reduced consumption and expense. When the pneumatic cylinders form part of a superior industrial automation systems enterprises reap major benefits in terms of efficiency, productivity and profitability.
Therefore, no matter the kind of industry that is continuing to change, pneumatic cylinders will continue to play important roles in automation systems. For organisations that have visions to sustain specifically in such market, acquiring quality pneumatic cylinders is not only a requirement but a wise advancement to making remarkable outcomes.